Utilizing 3D printers in the automotive industry
Vibracoustic case study (Mělník, CZ)
Thanks to NVH solutions from the Vibracoustic plant in Mělník, cars are becoming quieter and more comfortable. Vibracoustic is a leading global automotive Noise, Vibration and Harshness (NVH) expert for the automotive industry and we will show you how TRILAB DeltiQ 3D printers help Vibracoustic in Mělník.
The plant in Mělník manufactures motor mounts for car manufacturers around the world to avoid unwanted noise and vibration from the motor. The production process of these parts is complex and requires a high level of precision with the creation of individual parts and their assembly. This is then reflected in the economically sustainable methods of the company with a low amount of scrap waste.
3D printing has completely changed the approach to product development
„Because 99 percent of prints are utilized directly in our production, this greatly increases production efficiency and quality control of outputs ,” states Luděk Rozmanitý, designer of jigs and moulds. And further describes the typical scenario at a number of other Czech companies:
„If we had to come up with a process different from 3D printing, everything would take longer. The first step would be the design of an aluminum jig, followed by the selection process of a tool shop, then about 4 weeks of waiting for a free workshop date and then delivery. In short, about 5-6 weeks of waiting going the traditional way. With a DeltiQ 3D printer, production usually takes only a few days from initial request to deployment.”
With the acquisition of the 3D printer, there has been a change in thinking about product development, naturally. „From the beginning, we had our mind set on machining. The moment a person has access to 3D printing, they have to completely change their way of reasoning and start thinking proactively. The fact that you have an iteration of the product in your hands within a few hours and that you can work on another iteration right away helps. All this and 3D printing only further increases efficiency - it also reduces the complexity of product and material consumption as well as printing time,” adds Luděk Rozmanitý.
„From the beginning, we had our mind set on machining. The moment a person has access to 3D printing, they have to completely change their way of reasoning and start thinking proactively.” - Luděk Rozmanitý
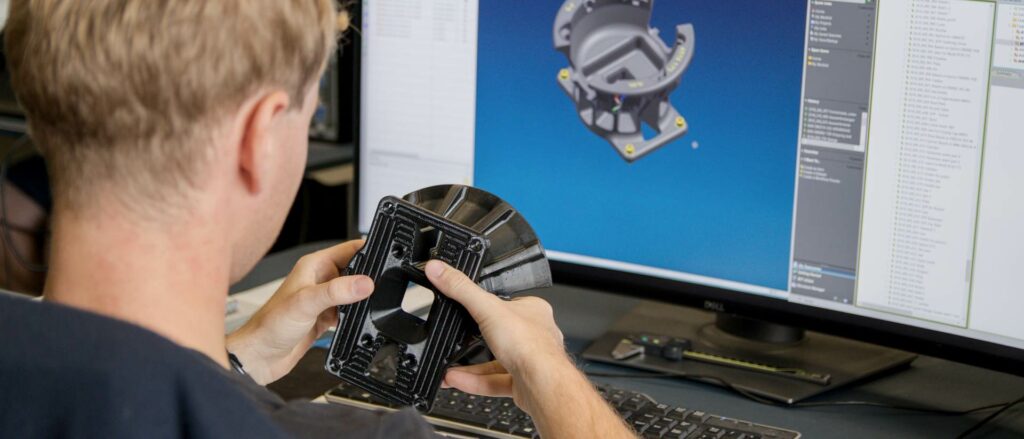
What about the longevity of plastic products? The DeltiQ printer at Vibracoustic mainly prints with low-cost, mechanically resistant PETG material. Printed stackers have now been used on the assembly line for two years in a row, and defects are rare and usually out of the operator's negligence rather than wear and tear.
Another undeniable advantage of in-house 3D printing is when a replacement is needed. It is possible to optimize the size of the spare parts warehouse and further print ad-hoc on demand within a few hours.
3D printing simplified & sped up quality control, expanding the number pieces that can be tested quickly.
A typical example of increasing the efficiency of processes are devices for quality control of output, in this case, components for motor placement in cars. The previous method of manual inspection was far from effective, as described by Mr. Rozmanitý: „You held the part in one hand, and a thread in the other, which you then tried to screw into the controlled thread. It made exit control more complex and less effective."
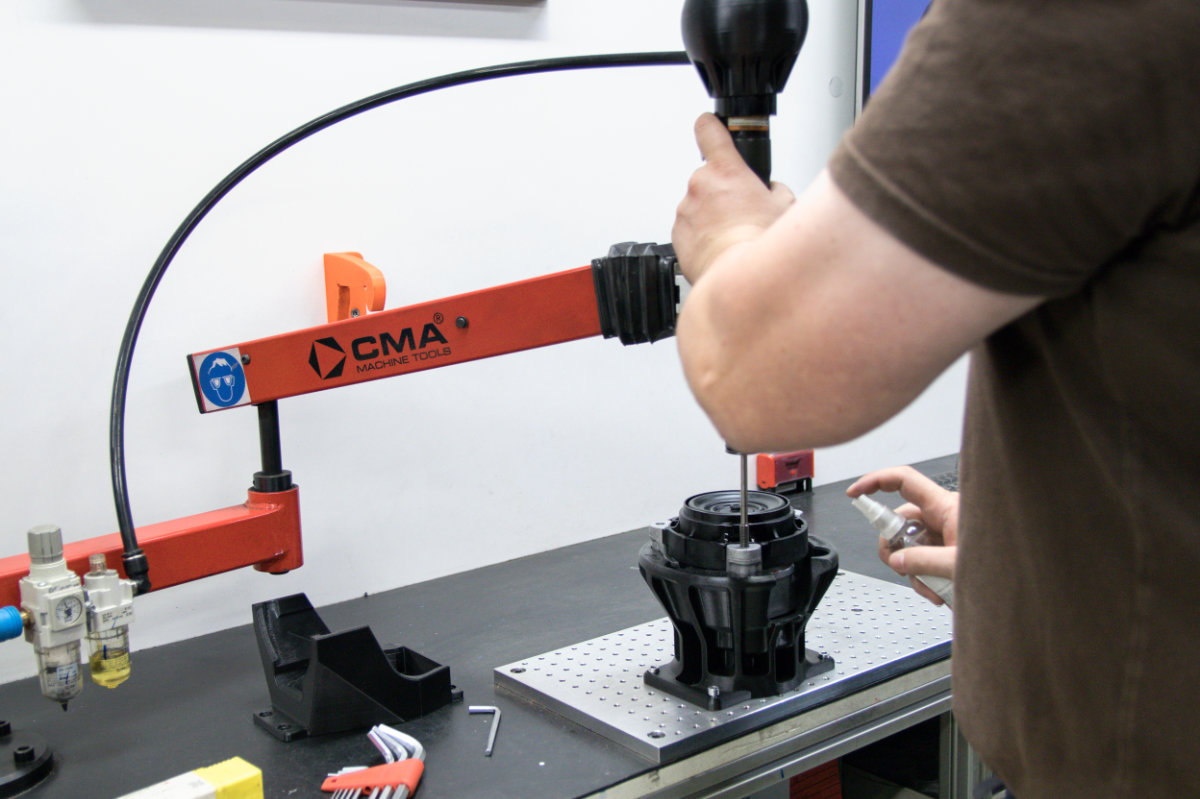
With the arrival of 3D printing, the inspection department switched to pneumatic thread inspection, especially with the requirements to create many variants of part positioning jigs that firmly seat each component on the workbench and allow its quick inspection. Now normally on the second or third day with overnight printing. „Productivity is now on a completely different level from the former manual control method. Swapping products for a different production line is now just a matter of loosening four screws,” adds Luděk Rozmanitý and within a minute, proceeds to replace a 3D-made stand with another.
„Productivity is now on a completely different level from the former manual control method. Swapping products for a different production line is now just a matter of loosening four screws,” adds Luděk Rozmanitý
By the way, you can also see the printed tester arm holder and its ergonomic head in the picture. You will find a number of similar aids within the plant facility.
The use of 3D printed products had a direct impact on production efficiency and on the overall profitability of production
Products made from 3D printers are not just "pieces of plastic", as it might seem. In combination with other materials and construction procedures, Vibracoustic has acquired a tool that directly affects production efficiency.
It’s an insert preparation into the molds of a vertical vulcanizing press. It is used to insert plastic rings and metal cores into the press, where it is connected to the rubber.
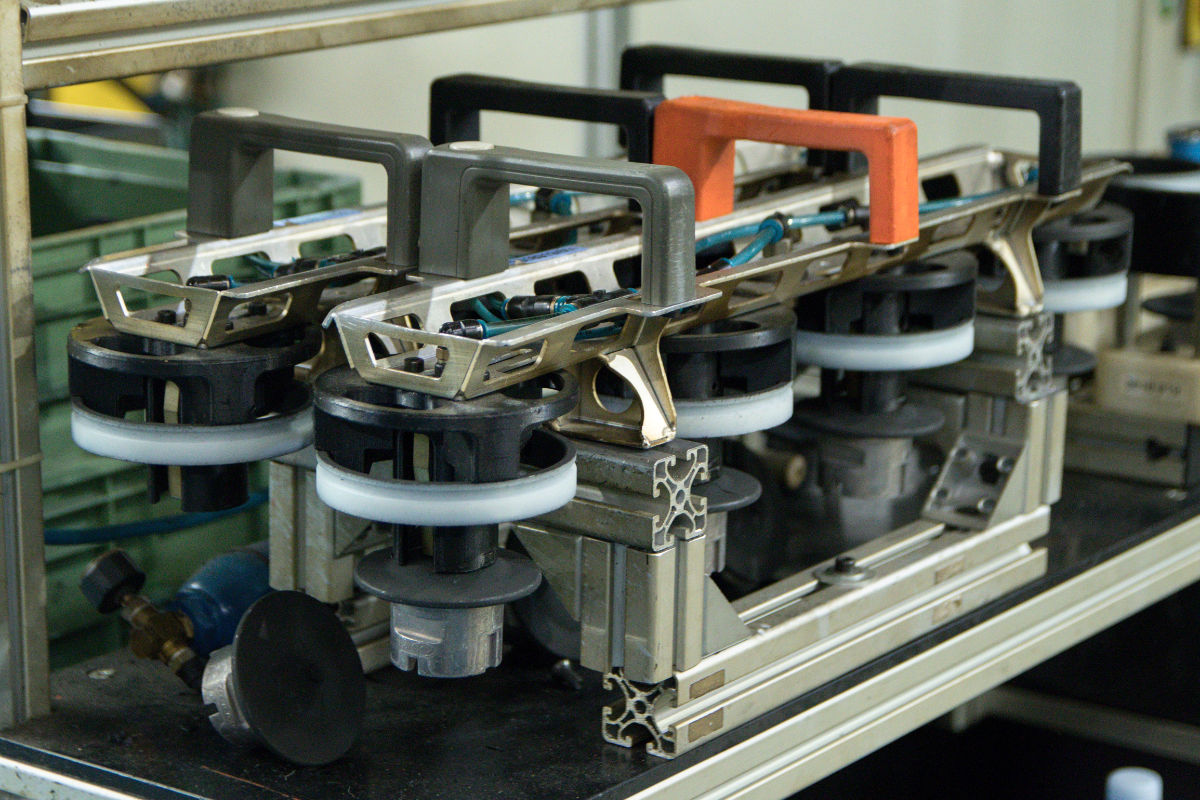
The product itself demands admiration with its intuitiveness. It is a combination of a universal metal bar, a closed pneumatic circuit and in-house developed and optimized nozzles, produced by the TRILAB DeltiQ printer.
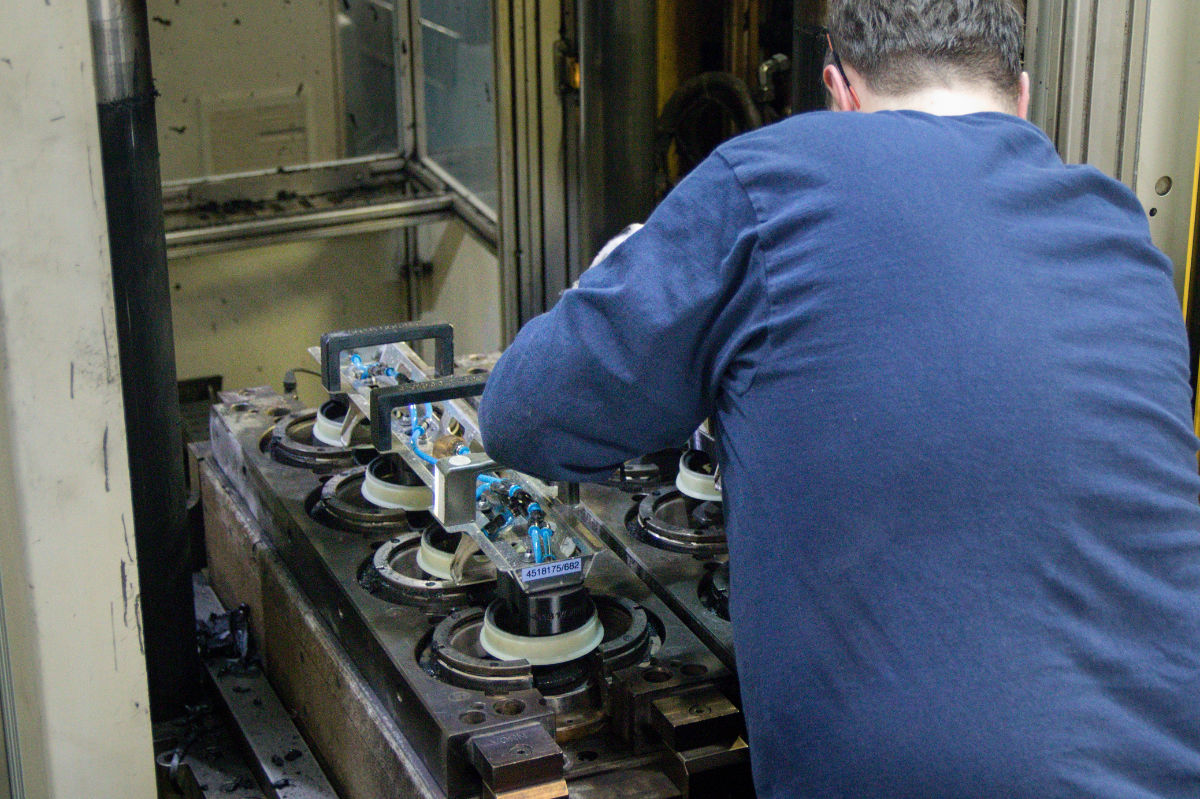
As explained by the designer Luděk Rozmanitý, „By bringing compressed air into the jig, the collected components are fixed and easily transferred to the press in bulk. The components can be prepared in advance on an auxiliary bench again with the help of 3D printing, which not only shortens the total time of one production cycle, but also increases the stability of the process, which is much more cost-effective than simply accelerating production."
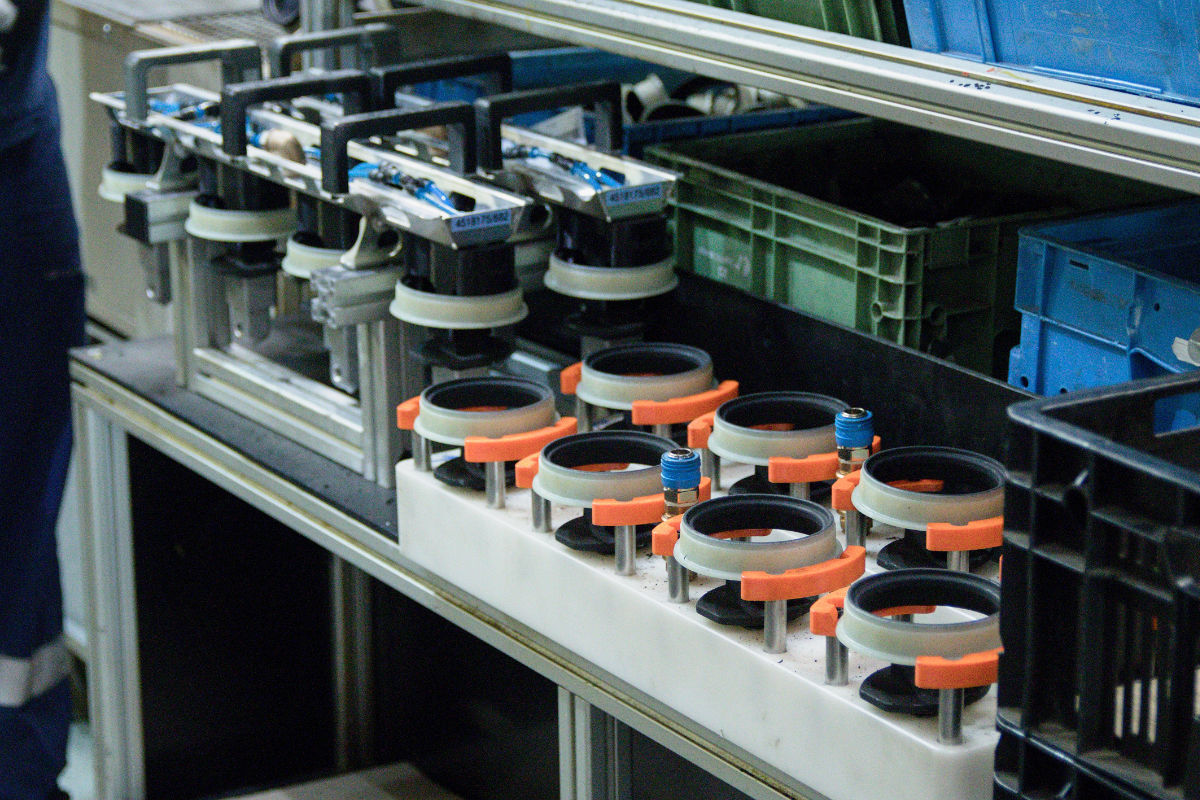
Thanks to 3D printing, the interval between pressing cycles is shortened, perfect placement of components is ensured and errors due to negligence are minimized. In addition to higher productivity, any deviations in the quality parameters of products are also reduced. As it was practically calculated directly in the production, the use of jigs shortens the entire cycle depending on the complexity of the part by 5 - 15%. As product complexity increases so does the benefit. Due to the production volumes, this creates a significant increase in process efficiency.
In addition, thanks to the availability of 3D printing, the design office can easily prepare other types of jigs for different product models and put them into production within just a few days. Luděk Rozmanitý contrasts this progression with the past when they worked without 3D printing: „It is unrealistic to design such a product from aluminum, for example, to tender a tool shop, wait 4-5 weeks for its delivery, and only then to test and change the parameters of the handpiece. We would only be able to propose a maximum of several variants per year. Within a year, instead of two variants, we managed to test and debug over fifty variants. Without 3D printing, this product would not have come into being at all,” he adds.
„Within a year, instead of two variants, we managed to test and debug over fifty variants. Without 3D printing, this product would not have come into being at all.”
3D printing brought unexpected savings and completely new opportunities
Each of the previously introduced products will economically justify the acquisition of a 3D printer for the company, but its use goes even further. "After the production of the first 3D printed products, we suddenly began to see opportunities where 3D printing can help everywhere," states Rozmanitý, for whom the construction of preparations is a daily duty. Its created countless holders, ergonomic handles and delimiters that make work easier.
An interesting example is the production of a pressure gun holder and the application of a separator in the form of a press. With the initiative of work safety, a requirement arose for a stable location of the pressure gun.
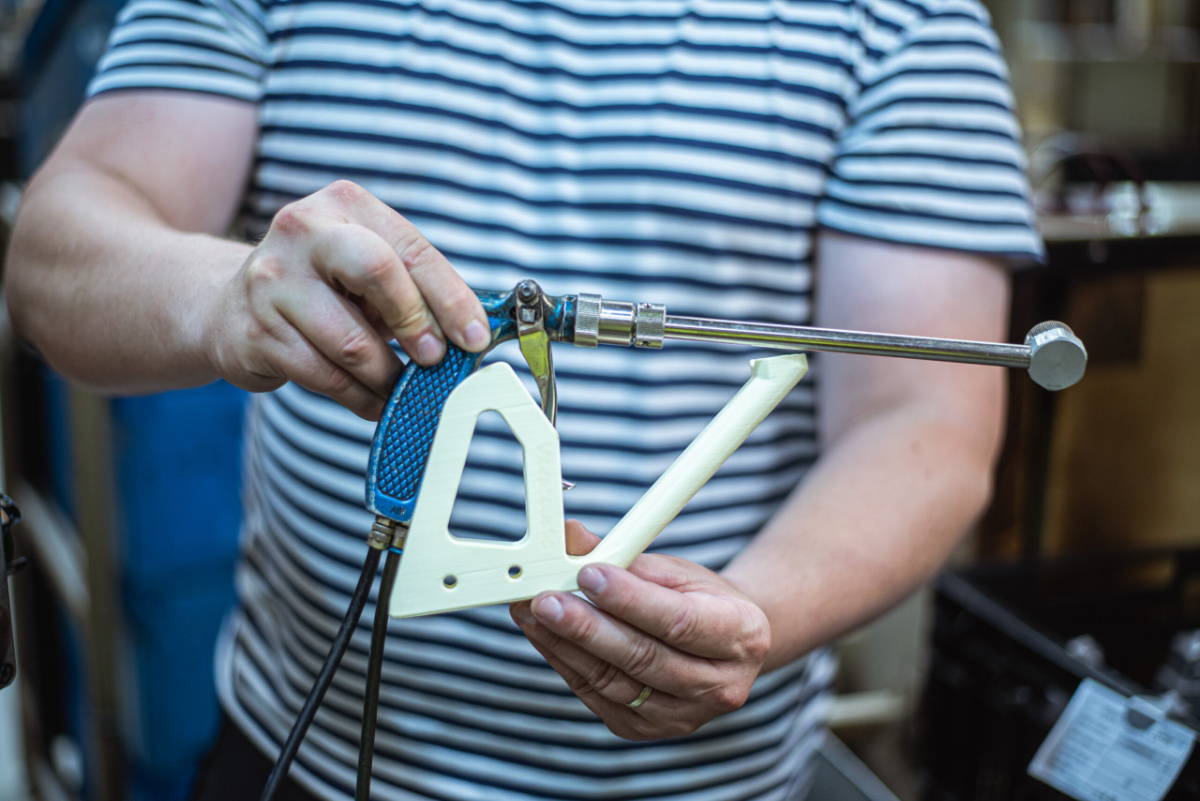
The first versions of the product were aesthetically pleasing, but because of 3D printing and the ability to quickly create several iterations, Vibracoustic soon worked out the final version of a simple handle that meets safety requirements and its production is fast and inexpensive.
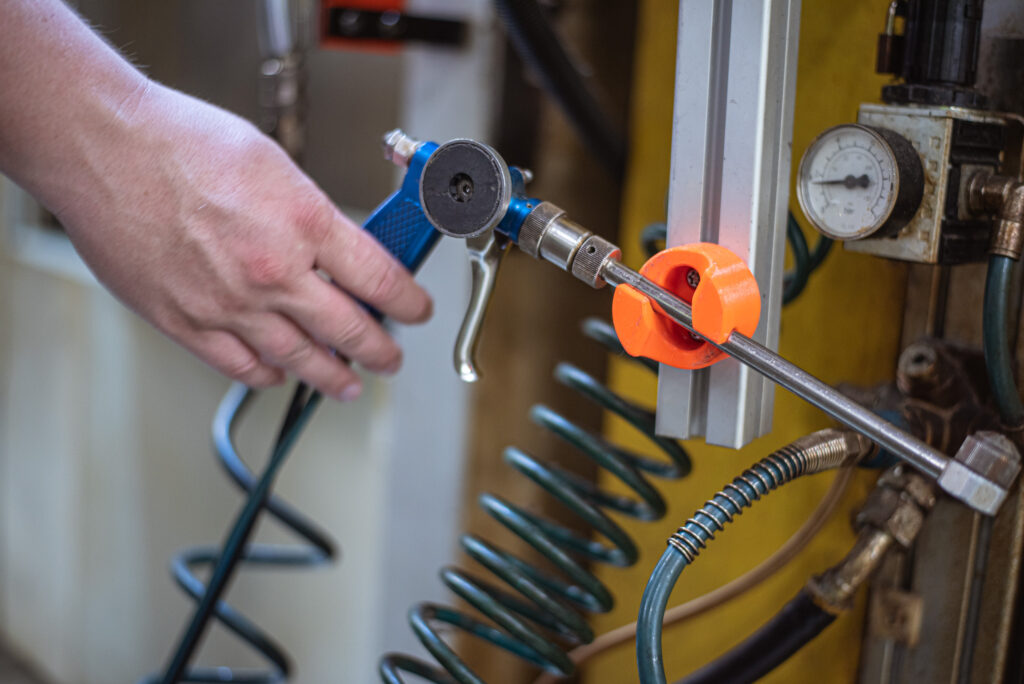
The end product would normally be manufactured using a different technology, but the entire development with fast iterations would be much slower and incomparably more expensive without 3D printing.
„The deployment of 3D printed jigs has reached the stage that during a year of operation we printed so many jigs, holders, stackers and everything (approx. 25km (72kg) of filament a year) that even though their service life is good with proper handling, the printer still basically worked nonstop with breaks only for service cases. That is why we agreed to purchase a second TRILAB DeltiQ 2 machine,” concludes Luděk Rozmanitý.
We can help with the deployment of 3D printing in your company too
Vibracoustic is just one of the many companies that we have helped with the delivery of a suitable 3D printing solution and its deployment. We have experience from engineering plants, automotive, casting, design offices, to production lines and scientific institutions. TRILAB DeltiQ jigs and models have already saved time and money at these businesses and workplaces. And even inspired prototypes, jigs and products that have never occurred to anyone with their own 3D printer.
Contact us by e-mail, telephone or via social networks and we will be happy to show you free of charge, how TRILAB 3D printers will help your company as well.